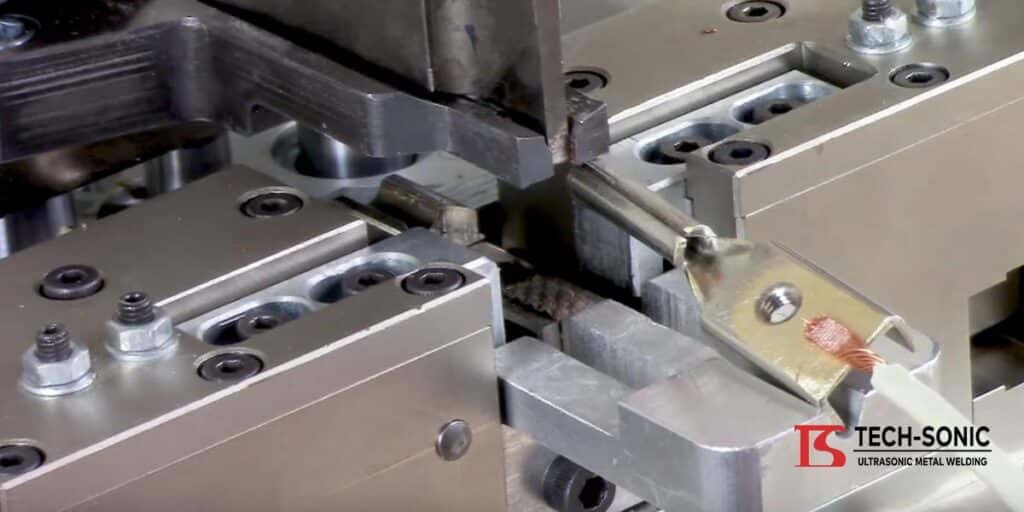
Difference Between Ultrasonic Welding vs. Conventional Welding
Welding is not new. It started in Egypt around 4,000 B.C. during the Bronze Age when soldiers fought with swords. The metals were heated and hammered into different tools.
This process remained unchanged until the early 19th century. By then, acetylene was discovered and used to heat the metal. In the middle of the 20th century, ultrasonic welding was discovered. It was introduced to bond metals quickly and at lower temperatures than conventional welding.
Related Topic:
|
What is Conventional Welding
Conventional welding is the process of joining metals by applying heat with or without the application of pressure or a filler. The most common techniques use are arc welding and oxy-fuel.
Arc welding joins metal to metal. It uses an electric arc that will generate enough heat to melt the material. When cooled, the molten metals solidify into a metallurgical bond. This method uses either direct or alternating current. It can either be manually guided or fully automated. Arc welding is popular in construction, welding pipelines, and repair of heavy equipment. It is also used in the fabrication of farm equipment, steel structures, ships, and vehicles.
Oxy-fuel welding is sometimes called gas welding. It uses oxy-acetylene flames to weld metals with high melting temperatures and oxy-hydrogen flames for metals with lower melting temperatures. Using a torch, this method is commonly used in factories and construction companies for small-scale welding.
What is Ultrasonic Welding
It is the type of welding that uses high-frequency ultrasonic vibrations. It can weld similar or dissimilar materials quickly and efficiently. There is no need for unsightly bolts, nails, solder, or adhesives. Ultrasonic welding is the top choice for clean, reliable, and precise joints.
You may also Like: Ultrasonic Welding Technology: What is it for?
Advantages and Disadvantages
Both conventional and ultrasonic welding has their pros and cons. It all boils down to the manufacturer’s quality standards, preferences, and materials used. The number one consideration should be to manufacture consumer-friendly products at lower production costs. More importantly, welds should be tough enough to withstand pressures.
The following are the more common reasons for using these methods:
Advantages of Conventional Welding:
- More affordable if you work with metals, or when repairing or welding tubes and ducts.
- The equipment is generally portable and easy to transport.
- Welds even when the metal surface is dirty.
Disadvantages of Conventional Welding:
- A protective shield or slag is necessary when using oxy-acetylene fuels.
- The heated joints are usually weakened or distorted. This method hardly works with thin metals, such as aluminum.
- It is not cost-effective due to prohibitive energy costs. Also, conventional welding produces a lot of material scraps.
- Arc welders need to be more skilled than most welding operators.
Advantages of Ultrasonic Welding:
- It is cost-effective. Even if the equipment is pricier than most, it only needs minimal energy compared to conventional welding. No connective materials such as bolts are necessary, reducing material costs. It is not labor-intensive, effectively lowering the overhead costs.
- An ultrasonic joint is stronger compared to traditional welds. The joints are practically invisible, clean, and dimensionally accurate since the materials are not deformed, saving the manufacturer on waste materials.
- The welding process is remarkably quick. It welds the materials in seconds, resulting in the rapid fabrication of products.
- Since the welding process is precise, the handling of the equipment is very safe. There is no excess oxy-fuel or electrical energy. It reduces errors and damage to nearby areas, including sensitive instruments.
- It is applicable for dissimilar materials and can easily bond metals to plastics or weld thick to thin materials.
- Ultrasonic welding equipment is reliable, particularly those that are automated or have minimal human involvement. Welding errors are not an issue.
Disadvantages of Ultrasonic Welding:
- Like all welding methods, it is not appropriate for all types of materials. It is particularly true for materials that have higher moisture and thicker dimensions, around 9 inches or more. It is most appropriate for overlapping joints and not on corners or edges.
- The equipment may need modifications to the current manufacturing process, meaning sufficient lead time. It could be an issue for factories with smaller areas with continuous production.
- More capital investment is needed compared with conventional welding, especially if the process is fully automated.
Why Use Ultrasonic Welding Methods?
There are many advantages to using ultrasonic welding over traditional methods, and these advantages more than outweigh the disadvantages. It is ideal for many industries, especially those that are involved in thermoplastics and light metals.
Whether you are already working with or planning to utilize ultrasonic welding in your company, TECH-SONIC has a quality range of ultrasonic metal welding equipment that could give you the required edge against your competition.
Related Posts:
Featured Products
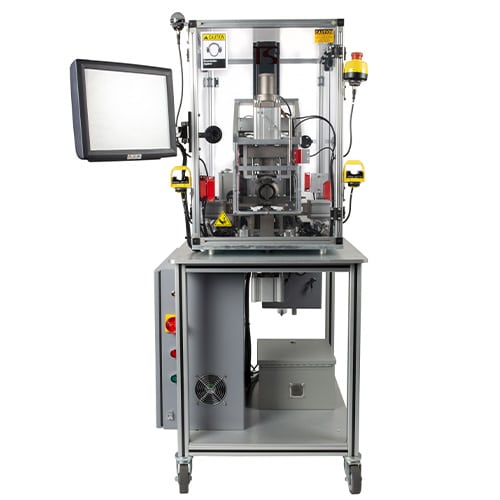
CLC Large Cable Termination Welder
US-3620STH
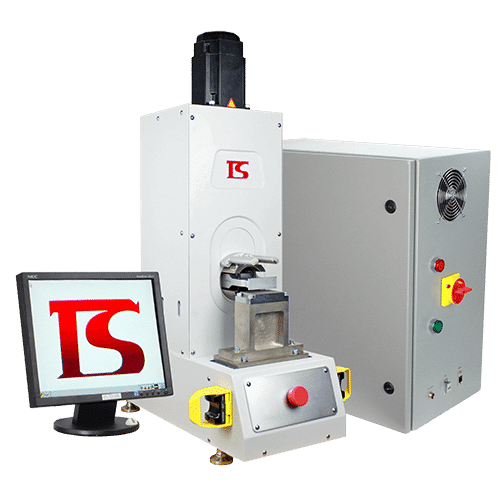
CLC Pouch/Prismatic Battery Welder
US-3620SH
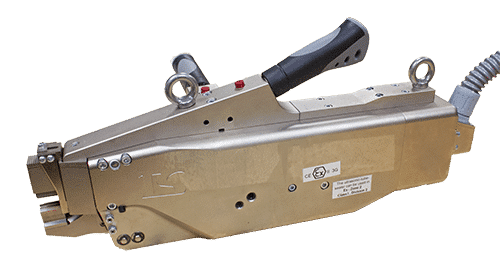
Ultrasonic Tube Sealer (Explosion Proof)
US-3620TS-EX