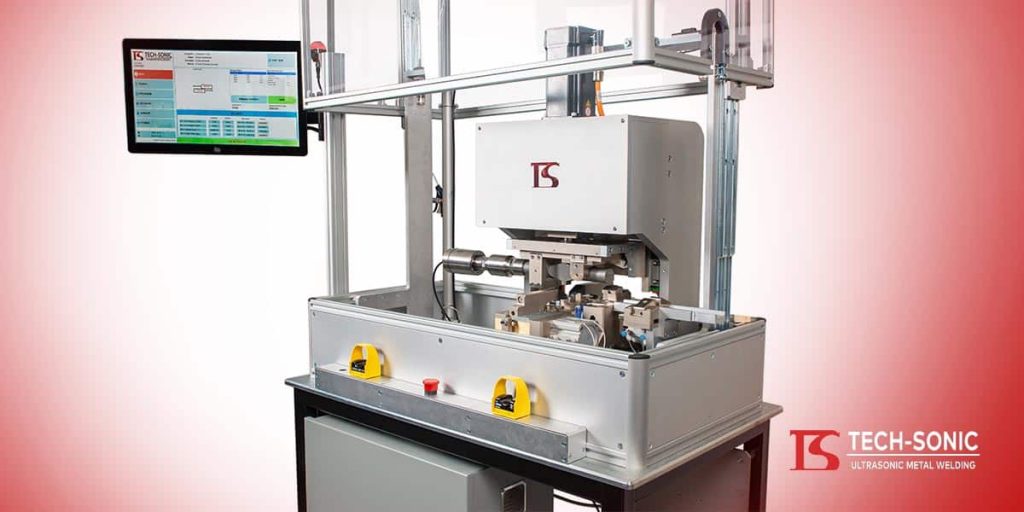
Unique Ultrasonic Welding for High Voltage Cables
- TECH-SONIC
- March 8, 2023
TECH-SONIC has been at the forefront of the ultrasonic welding technology since 1996. They have devoted themselves exclusively towards the manufacture of welding equipment and associated tooling on a global basis.
More recently, the company has focused development and manufacturing efforts into what they refer to as Closed-Loop Control “CLC” and they claim it’s the “Holy Grail” of ultrasonic welding technology. As the pioneer in this technology, TECH-SONIC has integrated the latest electronics, hardware, force sensors and control software in new and unique ways to improve the welding process.
We sat down with John Hall, Marketing Director at TECH-SONIC to discuss what differentiates their technology from their competitors.
“Our overall approach with CLC is what makes our equipment different. Our competitors operate on a pneumatic cylinder, whereas our equipment is servo controlled.” — John Hall stated.
“With that, you get total control of the welding process. It’s going to be much more reliable, more repeatable and perform welds with greater precision.” — John added.
An important part of TECH-SONIC’s Closed loop control technology is the ability to pre-heat and pre-clean the material before they do the weld.
“It’s all part of our multi-step process and it happens in milliseconds as the welder makes contact with the material,” — John described.
CLC Ultrasonic Welding Process for High Voltage Cables
-
- In step one, the horn proceeds from the starting position towards the wire. Once in contact, the system compresses the material in order to measure the height prior to welding.
- At step two, the horn applies a lower “scrubbing” amplitude that softens the material.
- Step three provides for a new force and amplitude.
- In the final step, the equipment sets the final weld condition and reports the after-weld height providing a weld quality test prior to the horn release.
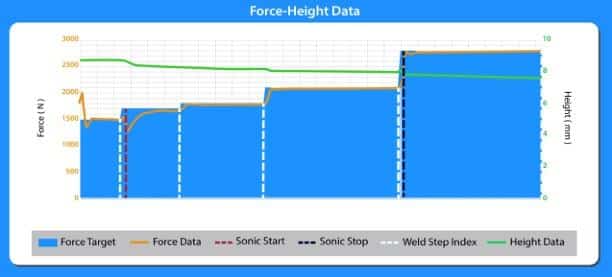
Figure 1. A great graphical representation of exactly what is happening during a weld.
“Our tooling lasts at least two to three times longer than our competitors because, as noted, we are softening the material before the weld. Also, the servo technology preforms a gentler landing on the weld material. With pneumatic you are coming down on the weld with more force whereas ours is a very controlled movement.”
“On some applications we work with, our competitors tooling was lasting 200k to 300k welds where ours was lasting over 1M cycles.”
“So, for high voltage cables of 95 mm², it only takes us 6 kW of power compared to our competitors who may be using 9 – 14 kW.”
“We are the only company today that complies with USCAR 38, and it’s something we are proud to talk about. The 5% missing strand detection rate is especially important when it comes to welding high-voltage cables in electric vehicles. The USCAR 38 compliance is a game changer for the automotive realm, and a great area of focus for them presently.
Right now, John and the team at TECH-SONIC are very excited to promote CLC technology as it pertains to high-voltage cable welding and busbar termination.
John and the team at TECH-SONIC will be on hand at booth # 1227 at the EWPT Expo in Milwaukee this May. He encouraged folks to stop by for a demonstration. In the meantime, you can see TECH-SONIC’s technology in action on their YouTube account.
Related Topics:
Featured Products
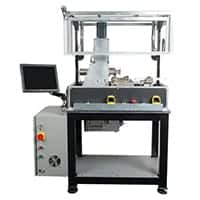
CLC Busbar Termination Welder
US-6020FWB
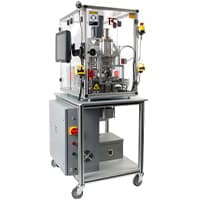
CLC Large Cable Termination Welder
US-3620STH