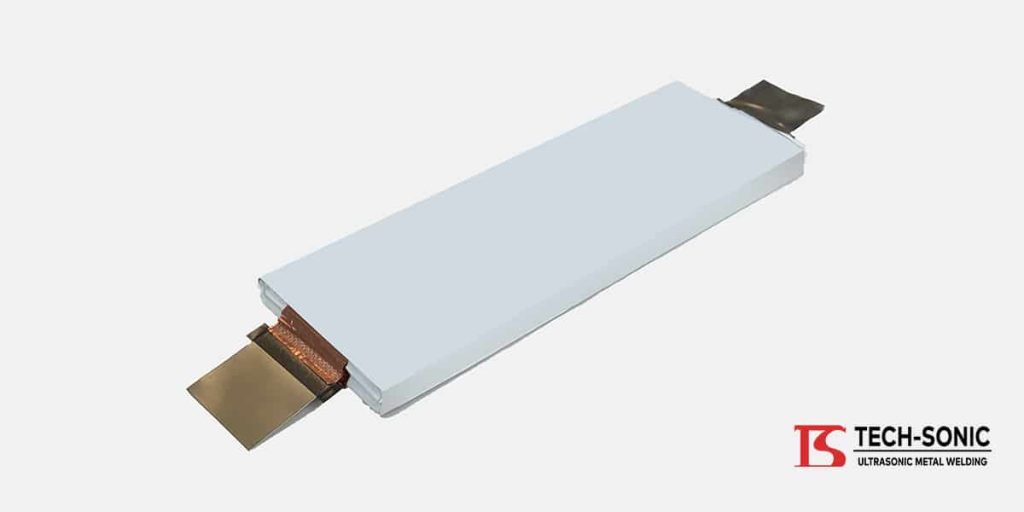
Advanced Lithium Ion Battery: Advances in Welding EV Batteries
The term “battery” was first coined by Benjamin Franklin in 1749. It describes a string of capacitors in his electrical research and used later when Alessandro Volta created the first battery in 1800.
What is a Battery?
In modern times, a battery describes a collection of one or more electrochemical cells. It can power electronic devices such as smartphones. Its electrical energy is stored in a portable case.
Two types of batteries:
- primary (disposable)
- secondary (rechargeable).
In the 20th century, batteries have different chemistries and come in all shapes and sizes. In 1985, Asahi Chemical of Japan built the first lithium-ion battery. While Sony developed the first commercial lithium-ion battery in 1991.
Without a doubt, this Lithium-Ion battery is in high demand right now as the demand for electric vehicles rises. Here’s an article about EV Battery Innovation; developing new technology necessarily requires a very well strategy in order to fulfill the demand for more efficient EV batteries.
What is Lithium Ion Battery?
EV battery operates an electric vehicle, designed for a high power-to-weight ratio. The most commonly used type is a lithium-ion battery. This lighter and more compact rechargeable battery power electric vehicles over prolonged periods.
The lithium-ion battery is intentionally lighter to reduce the vehicle’s weight. It is projected that electric vehicle adoption will increase in the coming years. User considerations include lower prices and an improved all-electric range of the vehicle. There is a need to overcome the current limitations of lithium-ion batteries.
Lithium Ion Battery Development
Industry leaders are working hard on EV battery development in order to have a fast-charging, high-density, and advanced lithium ion battery. Despite their increased range, EV batteries take several hours to recharge. This is inconvenient compared to the much shorter fuel stops needed for internal combustion vehicles. This is unappealing and should be improved. The question is how?
Industries are exploring the use of lithium-ion cathodes from cheaper resources. This includes lithium iron phosphate, lithium-sulfur, and niobium oxide. Each has its pros and cons and is still in the process of development. What is important is that these are efficiently produced at a lower cost.
Welding Advanced Lithium Ion Battery
Most manufacturing industries use ultrasonic welding in welding lithium-ion batteries. The ultrasonic spot welding method uses high-frequency ultrasonic vibrations to weld similar or dissimilar materials. Reliable standards for welding an advanced lithium ion batteries are one of the key components in manufacturing electric vehicles.
Among the first to develop a highly-advanced servo-controlled ultrasonic spot welding machine for advanced lithium ion battery assembly is TECH-SONIC, Inc. It uses the Closed-Loop Control welding process which combines ultrasonic welding, servo control, user-friendly microprocessor control, and load cell force feedback. This 100% digital welding process is the top choice for clean, reliable, and precise welds.
It creates solid-state welds between foil stacks, foil-to-tab, foil-to-busbar, and tab-to-busbar to meet the needs of welding lithium-ion batteries. TECH-SONIC’s 3.6kW US-3620SH ultrasonic spot welding machine can detect one single missing or added foil in a stack of eighty (around 80um). It then signals the error to the user before initiating the welding sequence. Traditional pneumatic welders do not have such a precise foil detection capability.
By applying optimum force and energy through Dynamic Force and Amplitude Control™ end-users can weld larger stacks of foils with a wider weld area. Whatever your requirements, TECH-SONIC, Inc. has a wide range of ultrasonic metal welding equipment to optimize production needs.
Featured Products
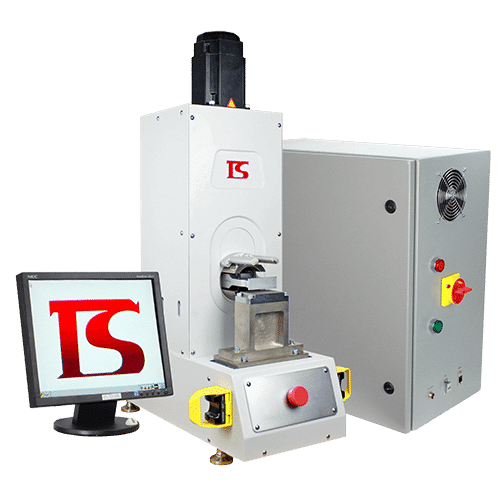
CLC Pouch/Prismatic Battery Welder
US-3620SH
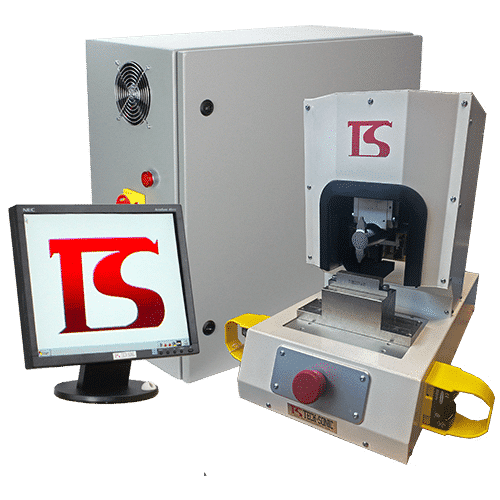
CLC Cylindrical Battery Welder
US-935SH